Last Update: September 22, 2023
About Proximity Manufacturing Company
Overview
White Oak Legacy Foundation, Inc. established Proximity Manufacturing Company in 2021 as a for-profit subsidiary that will operate as a textile manufacturing arm of the non-profit organization. Operations are based at the former White Oak Plant, first opened in 1905 in NE Greensboro. Denim Manufacturing adds breadth to educational programming, offers skilled workforce development and employment opportunities, and allows WOLF to become a pillar in the community through historical preservation of the very cloth that wove our city together and built a 125+ year legacy for Greensboro.
How Our Denim is Made
You cannot build a superior product without using the best inputs available. We sourced our warp yarns from Mount Vernon Mills (MVM), the last American denim giant. We hired former Cone employees with decades of experience.
Well, that’s our recipe, no need to read any further!
…just kidding!
US-grown ringspun cotton yarns from Parkdale arrive to MVM’s Trion, GA denim plant, where they are loaded onto creels and balled together into ropes of approximately 400 ends (individual yarns). These ropes then head over to the dyehouse, where they are loaded into a dye range, passing through several dye boxes filled with indigo dye, and rising high up into the room to oxidize between each dip. On the back end of the dye range, the now dyed, roped yarns are coiled into containers, then passing over to the rebeaming department where they are “un-roped”, taken out of rope form and laid individually onto smaller beams, side by side. These smaller beams, known as section beams, are sent over to the slashing department, the most critical process with the blue yarn that truly makes a denim. In slashing, six smaller beams are combined together as they feed in, passing through a range that applies starch to the yarn for strengthening, a necessary step to weave singles, preparing it for weaving. Slashed indigo-dyed warp yarns are wound onto loom beams at the end of the slashing range, and are now ready for us to begin the weaving process.
We make the long, roundtrip journey to Trion, where we pick the beams up and truck them back to White Oak Plant in NE Greensboro. The beams are then loaded into the let-off side of the looms, and the ends of the previous warp are meticulously tied onto the new warp ends using an automated tying-in machine. Sometimes a few get crossed, or a knot fails to tie, and we have to stop the machine and knot a few by hand, but for the most part the tying-in machine saves us a lot of time and labor. Once tied and inspected, we crank the yarns through the drop wires, harness heddles, reed, temples, around the sand roll and presser roll, and onto the take-up cloth roll. Now, it’s time to begin weaving!
Simple enough, right?
Shuttle-Woven
Our shuttle looms were originally built by Draper Corporation, a Hopedale, Massachusetts-based textile equipment manufacturer, sometime during the 20th century, and spent the last several decades inhabiting the wooden floors in White Oak Plant. At some point, they were modified into their current size, being cut down from a much wider frame, and their retrofitted and replaced parts make it nearly impossible to give them an exact age. We further modified our machines by reinstalling original take-up motion sets, consisting of a series of gears, sprockets, spring load, and a chain drive that allows a cloth log to be placed onto the loom that winds the finished denim directly up onto it, forming rolls approximately 20” in diameter. These shuttle looms slowly weave at about 170 picks per minute, a reference to the number of throws of the wooden shuttle, filling the warp and thus creating cloth. The cloth produced is narrow, measuring roughly 34” wide. Twelve natural yarn ends on each edge of the cloth, known as selvage or selvedge, are as iconic as they are subtle. In fact, this is the same number of selvage ends used when the mill first originally opened and began producing denim in 1905. The slow pace of the loom, coupled with the harmonic bounce it achieves being mounted on the old wooden floors, produces cloth with irreplicable character and timeless appeal.
If you’re still reading, by now you’re approaching denim nerd status.
Inaugural Cloth Production
Our warp yarns for this inaugural production were made from ringspun, US-grown cotton yarns, dyed in Canyon Blue, MVM’s name to reference a 9%, 9-dip shade of blue. It is very reminiscient of department store-branded western denim from the 1950’s in weight and shade. For filling, we have used several different 100% cotton ringspun yarns, all around the weight of a 10s. Woven in a 3x1 (4-harness) construction with a steep right-hand twill, the inaugural denim weighs in at just over 12 ounces per square yard, the perfect year-round weight. Our cloth is unsanforized, meaning it is not mechanically pre-shrunk using chemicals and a water-intensive process, reducing its overall environmental impact. It is loomstate, in the truest sense of the word, meaning we weave it, doff it, a way of saying remove it from the loom, and take it to inspect on a measuregraph machine. We inspect every inch of the material, front and back, and mark all major flaws and errors to help out in the cutting room. The denim is then wrapped in protective packaging, loaded onto pallets, and shipped to partnered brands. Finally, we work with partnered brands to fluently understand the “shrink-to-fit” nature specific to each of the fabrics we produce, and they produce garments with expected shrinkage taken into account, respectively.
Director’s Notes from 2023:
This year we have continued business as usual with MTO production, but we’ve also been heavily involved in R&D projects with a variety of companies, building breadth into our ability to operate a nimble micro-mill concept in a world of textile giants. We have spent countless hours making minute adjustments to our weaving equipment, honing in on our highest efficiency and augmenting production quality even more. Upstream, we have partnered on projects and with organizations for fiber, dyestuff, yarn, and construction developments. Last year, we were the first to produce a denim woven with US-grown, degummed hemp. We learned a lot in this project, working with industry first-movers to develop proprietary yarns and inserting them into our cloth construction. We’re excited for what the future has in store for us, whether it involves cutting-edge projects or building classic, standard denims. Stay tuned for more updates, or check out our social media page on Instagram here meanwhile.
Partnered Brands
Just here for the goods, eh?
We have proudly partnered with select brands, who have a like-minded focus on quality and integrity, to produce garments from our inaugural run of cloth. Click the links below to learn more:
Opie Way Footwear — Weft Out Sneakers
Runabout Goods — The Brander Jacket
Tellason — Straight Leg Jeans
HARDENCO x HUDSON’S HILL — 003 RHT
HARDENCO x HUDSON’S HILL — 003 LHT
First Standard NYC — 652
Stockbridge Sewing Works x FyberX — Cotton/Hemp Caps
Opie Way Footwear x FyberX — Cotton/Hemp Sneaker Concept
Hudson’s Hill x FyberX — Parka Concept
Contact Us
Email us at proximitymfgco@gmail.com with questions or comments. Please allow 3-5 business days for a response.
Want to follow our journey and read the Deeptone Diary? Check us out on Instagram, by clicking here.
Now, we’ve got to get back to weaving denim! Cheers.
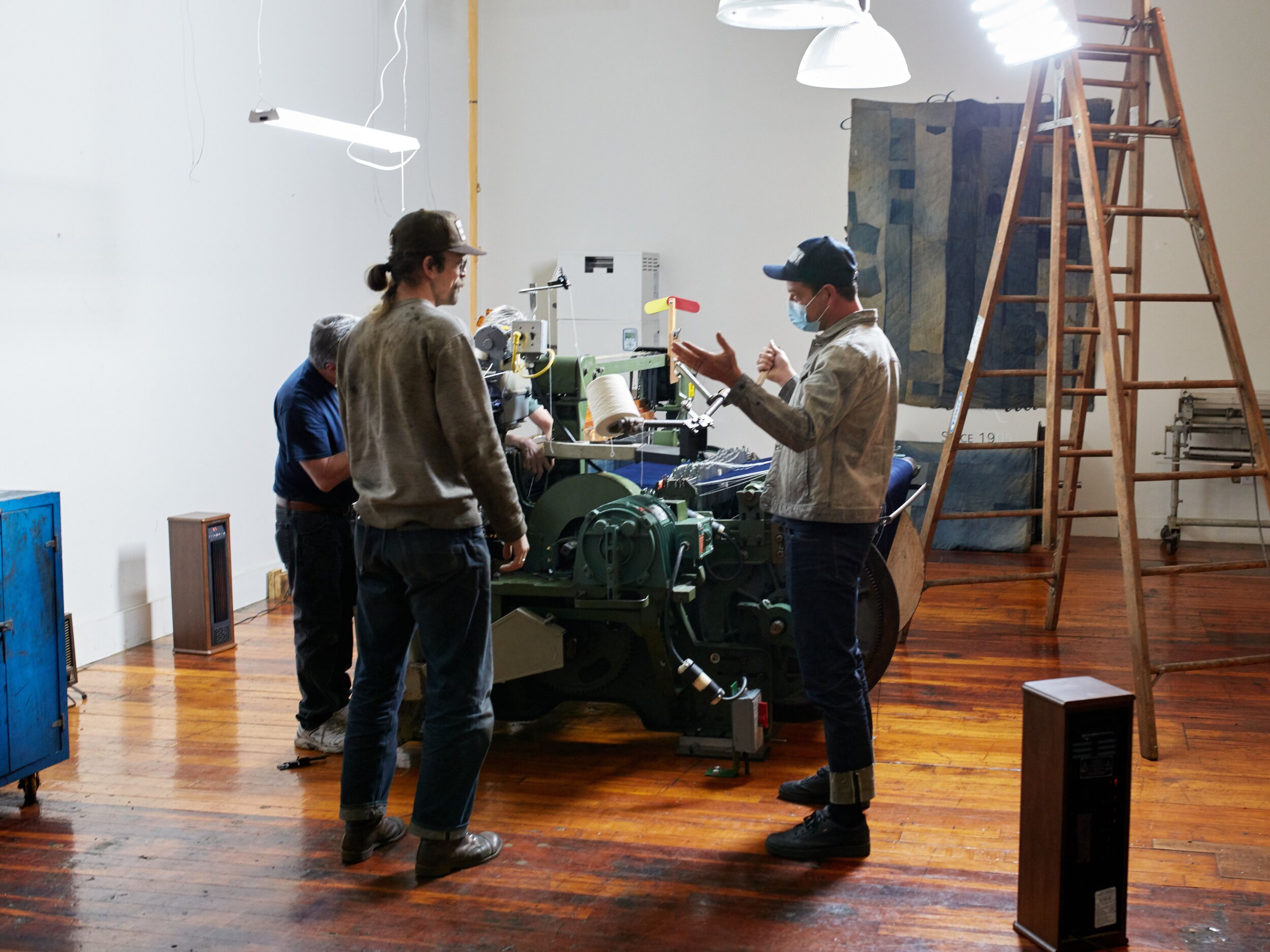
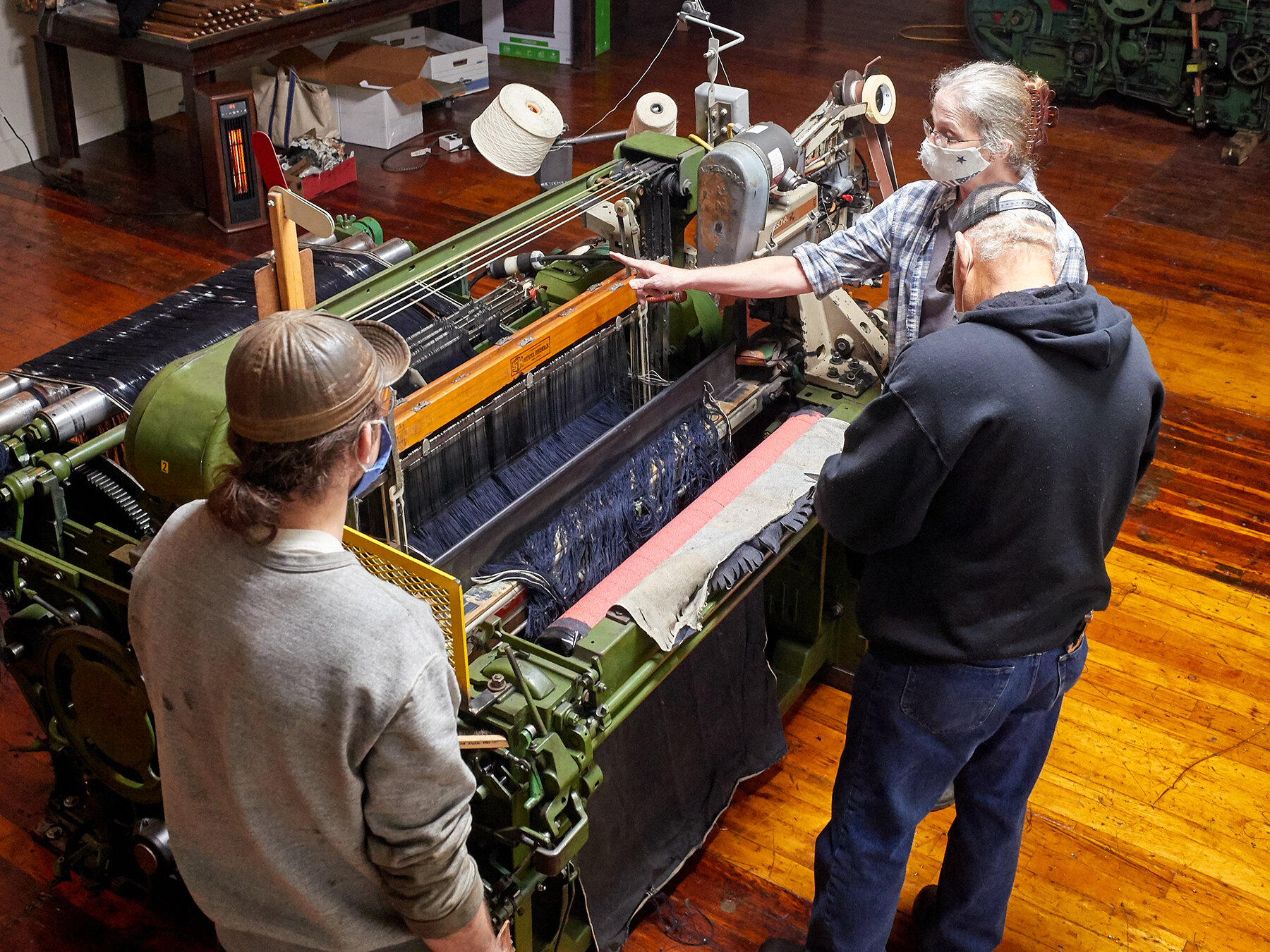
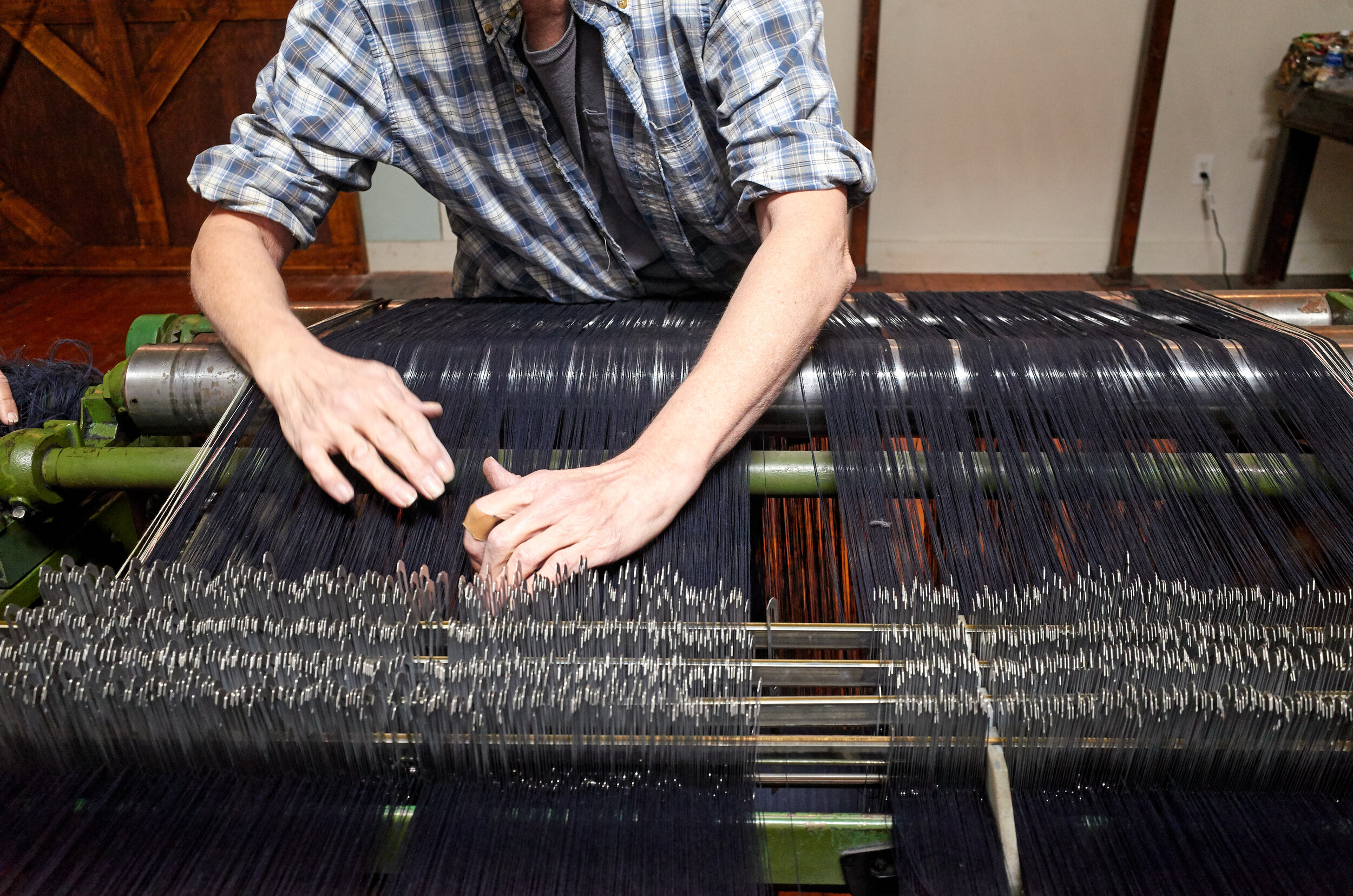